Injection Molding Static Mixing Nozzle (Type SMN)
The SMN Injection Molding Static Mixing Nozzle creates homogeneous mixing of polymer melt during injection. The resulting high viscous plastics melt flow is homogeneous with regard to colorant, additives and temperature. |
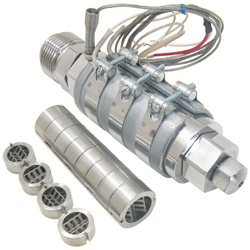
Figure #1: SMN Injection Molding Static Mixing Nozzle with 8 very efficient SMN Static Mixing Elements |
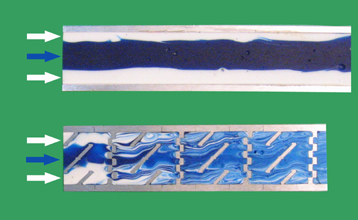 Figure #2: Empty nozzle (top) provides no mixing. Eight (8) SMN Mixing Elements (bottom) create homogeneous mixing in a short length. |
Benefits
Outstanding melt flow mixing of molten polymer prior to injection results in the following benefits: |
- Reduced spots, streaks and clouds of color
- Reduced colorant usage (10% - 40%)
- Narrower part tolerance
- Reduced reject rates
- Less part distortion
- Less weight variation
|
- Improved part quality when using regrind material
- Shorter cycle time
- Improved melt flow
- Increase regrind ratio with consistent product quality
- Rapid nozzle heat-up
- Normal Pay-back period of 2-3 months
|
More Information
Technical Bulletin (pdf 411 kb)
Movie (wmv 1.14 MB)
Customer Specification Questionnaire (Excel 34 kb)
Operating Instructions Manual (pdf 707 kb) |
Filter for Injection Molding Static Mixing Nozzle (Type SMF)
The optional SMF Filter is installed inside of the Static Mixing Nozzle to protect the hot runner system and mold when processing regrind materials by avoiding clogging and/or damage with debris carried along with the feed pellets. |
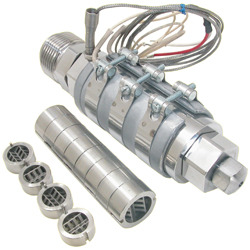 Figure #3: SMF melt flow filter for SMN Mixing Nozzle |
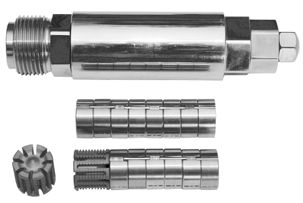 Figure #4: SMN Mixing Nozzle (top). Eight (8) SMN Mixing Elements (middle) and SMF Filter with 6 SMN Mixing Elements (bottom) |
Benefits & Function
The SMF Filter is designed to be used with the SMN Injection Molding Mixing Nozzle. The purpose and function of the SMF filter are numerous: |
- Protects hot runner system and mold by avoiding clogging and/or damage caused my metal pieces accidentally introduced with the feed pellets to the injection molding machine (staples, metal chips, paper clips, etc).
- Retains semi-molten polymer pellets until melted for incorporation into the polymer melt.
|
- For customers with poor thermal control systems, the SMF Filter acts as an upstream “breaker-plate” to prevent “cold-start” crushing of the mixing elements.
- Designed to retrofit into the SMN Injection Molding Mixing Nozzle without nozzle modification
- SMF Filter O.D. = SMN Mixing Element O.D.
- Length of one (1) SMF Filter = Length of two (2) SMN Mixing Elements.
|
More Information
Technical Bulletin (pdf 226 kb) |